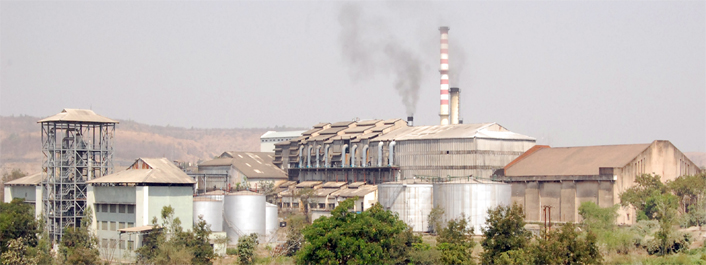
The Sugar Plant has a capacity to crush 4500 MT cane per day. Its salient features include optimum use of Auto Feed Control of automation in the plant helps in achieving better efficiency. The state-of-the-art Sugar Silo System which facilitates efficient cooling of sugar, is augmented with auto weighing and auto stitching of sugar bags.
Plant Details
- Initial Capacity 1250 TCD Capacity (1980-81)
- Supplied by M/s Buckau Wolf India Ltd., Pune.
- First Expansion from 1250 to 2500 TCD (1994-1995)
- Supplied by M/s Buckau Wolf India Ltd., Pune.
- Second Expansion from 2500 to 3500 TCD (1999-2000)
- Supplied by M/s. S.S.Engineers, Pune
- Third Expansion from 3500 to 4500 TCD (2012-2013)
- Supplied by M/s Thamson Krup Ltd., Pune., Skylark Sangli, Hightech Baramati
Special machineries had installed at Boiling House :
--- 1.Syrup Clarification System
- During the Season 2014-15 the Syrup Clarification system was commissioned and erected by Diftech India Ltd. New Delhi. Because of this system , we have achieved colour reduction of syrup, enhance transmittancy of syrup, turbidity removal and CaO removal , ultimately the physical appearance of sugar also improved.
- 2.Clear juice pressure filter unit
- To avoid bagacillo particles in sugar, we have installed clear juice pressure filter unit at delivery line. Because of the fine screen having hole size 150 to 175 micron bagacillo particles were separated. The screens of this filter unit was cleaned after every 40 hrs. to remove deposited bagacillo. This was very useful to the industrial buyers like Pepsico who were facing problem during their melt filtration, previously.
- 3.Vapcon Unit for Sulphur Burners
- Previously 100 lbs live steam was used to prepare the melt of sulphur. After installation of Vapcon unit for Sulphur Burners the sulphur is melted from waste heat from the temperature of SO2 gas before its cooling. Due to this 100 lbs. steam is completely stopped and this results in reduction of Steam consumption.
- 4.Pan Automation
- We have installed pan automation system which related to brix, steam feed control, mass cutting, vacuum break, steam washing, condenser valve operation is controlled automatically. Because of this efficiency of Pan Station is increased.
- 5.Decanter Unit
- This unit we have installed for separation of filtrate and mud. Generally while using oliver vacuum filters for separation, bagacillo is required. But when we are using decanter unit no bagacillo is required and saving of bagasse is at 1% on cane which helps to prolong the working day of co-generation unit. The electricity requirement is less as compared to oliver vacuum filters. Also sugar loss in pressmud is less as compared to oliver filters and it is consistent.