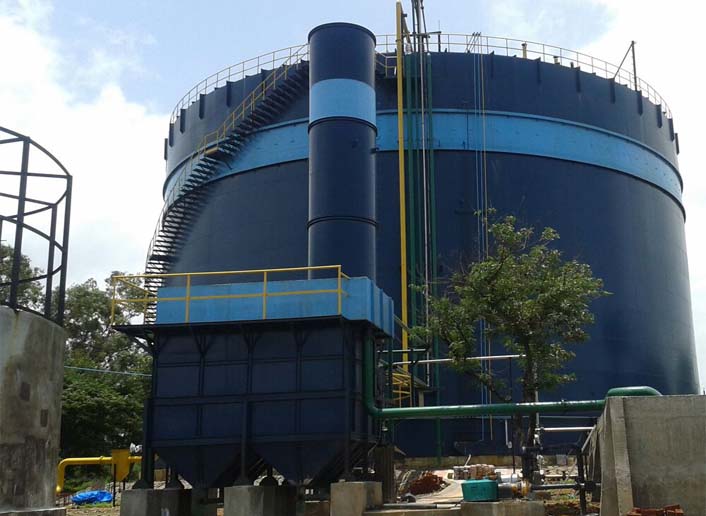
While manufacturing Rectified Spirit in Distillery, the wastewater called Spentwash is generated at the rate of 7 to 8 liters per liter of rectified spirit produced. The disposal of spentwash is a very tedious job as it has acidic pH & very high organic content. For the reduction of organic content, anaerobic digestion of spentwash is being carried out in many distilleries, which in turn gives methane gas having good calorific value. The generated biogas can be burnt in boiler to produce the steam required for production of rectifier spirit.
Our factory decided to install bio-digester plant and placed work order to M M Enviro Projects P. Ltd. Nagpur in the month of April-2013. The Capital Cost of the entire project is around Rs.06.00 Crores. The Civil Work, Fabrication of Digester, Installation of mechanical equipments, hydro test for leakages, painting etc. carried out in a span of around 9 to 10 months. The commissioning initiated in March-2014 & supply of bio-gas generated to boiler started in May-2014. The trial of this plant has been successful & the plant is running with full capacity for the entire season. The biogas generation is around 20,000 m3/day which is equivalent to around 50 M.T. of bagasse. The payback period of this plant is around four years.
Manufacturing Process:-
This process is based on Continuous Stirred Tank Reactor [CSTR] which is called sulzer technology from Switzerland. In this process the effluent i.e. spent wash is fed to the digester. In digester, anaerobic digestion of spentwash takes place. The process is carried out in three steps i.e. Hydrolysis, Acidogenesis and Methanogenesis.
- i) Hydrolysis:-
- In this process the complex molecular compound i.e. polymers are converted into simple molecular form i.e. monomers.
- ii) Acidogenesis:-
- In this process monomers are converted in to volatile Fatty acids. Acetic acid forms the major portion of volatile fatty acids. The process of conversion of monomers into acid is carried out by group of anaerobic bacteria known as acid formers.
- iii) Methanogenesis:-
- It is carried out in temperature between 35-400C degree celcius. Acids produced at end of acidogenisis process are converted into carbon dioxide and methane gas. The process of conversion of acid into gases is carried out by group of anaerobic bacteria called methane formers.
- The CSTR Reactor is designed on the principal of anaerobic contact process. The effluent is fed from the top of the digester. Agitators are provided for mixing the effluent. The effluent travels to the bottom of reactor through central shaft. The effluent comes in contact with active biomass which is present in suspension. In the process the organic matter in the effluent gets converted into Bio-gas & cell mass. The liquid travels upward in the reactor & is taken out from reactor through overflow pipe line. The effluent is further passed through degasifying tower to remove dissolved gasses & then effluent enters into lamella clarifier. In lamella clarifier the active Bio-mass is separated & part of it is re-circulated to reactor.
- Biogas produced in the reactor is collected at the top of the reactor and stored in a gas holder which is separately constructed. After that it is sent to boiler for burning through gas blowers.
- iv] Final Product (Biogas) :-
-
Composition of Biogas-
- Methane :- 65%
- Carbon dioxide :- 32%
- H2S :- 2%
- Other :- 1%